Diesel Particle Filter Regeneration: Shorter Downtimes Thanks to Viscous Fan Drives
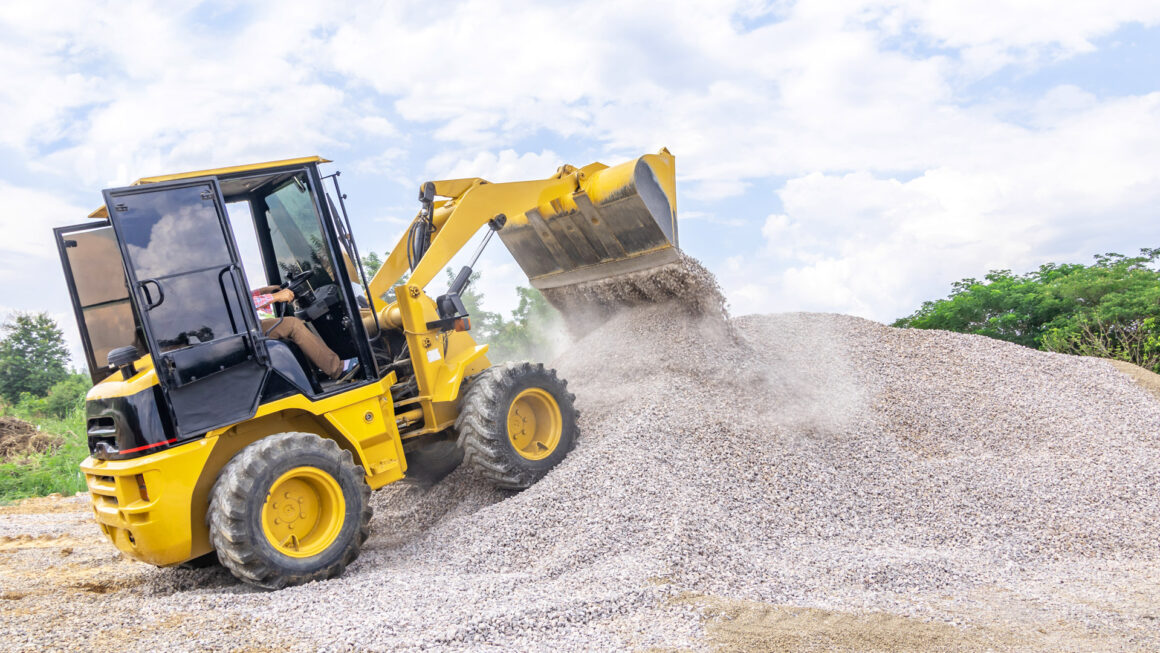
June 13, 2021
Frequent downtimes for active regeneration of the diesel particle filter are a nuisance for users of low-load commercial vehicles (up to 55 kW) in part-load operation. These downtimes can be significantly minimized by installing a variable-speed viscous fan drive. It ensures faster heating of the exhaust gas and engine temperature, which in turn leads to slower clogging and faster regeneration of the filter.
Since the Stage V emissions standard came into force in 2020, the use of a diesel particle filter in construction machinery has become unavoidable in Europe. This is because, unlike the previous exhaust emission standards, which were primarily concerned with limit values for carbon monoxide, nitrogen oxide, hydrocarbons and particulate matter, the Stage V standard includes a limit value for the number of soot particles. These are filtered out of the exhaust gases by the diesel particulate filter. Gradually, however, it becomes clogged and requires regeneration.
The problem with the DPF
But why does this happen? In many smaller commercial vehicles, direct drive fans are still installed. These always cool at full power as soon as the engine is running. However, they are designed for the “worst case”, i.e. very high outside temperatures of around 50-55°C and full load. Since this case rarely occurs, the engine is permanently overcooled and results in incomplete combustion of the diesel, especially during cold starts. Passive regeneration of the diesel particle filter, i.e. regeneration during regular operation, can hardly take place at low exhaust gas temperatures because the soot that builds up in the particulate filter can only oxidize optimally at high temperatures. As shown in the graph below, at exhaust gas temperatures of 600°C, the soot oxidizes quickly and completely. Even at 500°C, oxidation takes much longer and only about 80% of the soot is oxidized. At even lower temperatures, the duration increases and the oxidation rate decreases noticeably [Goldenberg 1983]. Additionally, customers with direct drive fans will experience frequent downtimes in order to actively burn the DPF free.
Improvements through a viscous fan drive
By installing a variable-speed viscous fan drive, the engine is cooled only when necessary. If the engine load is very low for a longer period of time or permanently, the viscous fan drive lowers the fan speed to achieve the optimum engine temperature and supports complete combustion. The regeneration of the diesel particle filter has the following effects:
By keeping the engine at optimum temperature at all times, the number of particles emitted is significantly minimized. Particles build up more slowly in the diesel particulate filter, and the time interval between regeneration cycles increase.
During a regeneration cycle, the engine reaches the optimal temperature for regeneration as quickly as possible because the fan speed can be reduced. The time required for a regeneration process is thus reduced.
Horton can help you find the optimal engine cooling solution for your application. The extensive portfolio includes various viscous fan drives and matching fans. In addition to the positive effect on diesel particle filter regeneration, variable speed viscous fan drives offer other benefits such as reduced noise operation and fuel savings. Request the support of Horton’s engine cooling experts for your project now!
You can learn more about variable-speed fan drives at hortonww.com/viscous. You can also watch back a recent webinar featuring Horton’s engine cooling experts discussing this technology.