Boost Your Engine Cooling with High-Quality Remanufactured Fan Clutches
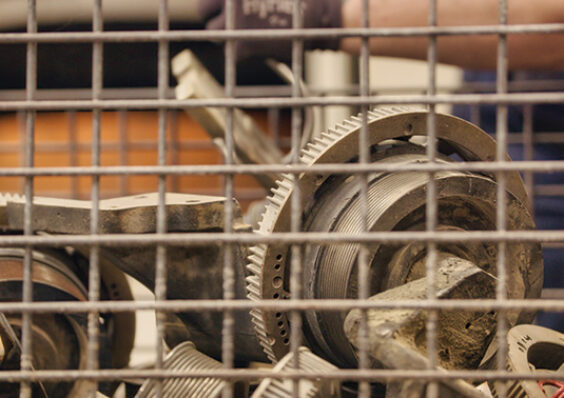
There is a misconception about the most efficient way to replace a damaged fan clutch in the trucking aftermarket. Many believe that rebuilt kits are the best option; however, this is no longer true. The market is shifting towards remanufactured parts as a viable alternative as it’s being learned, these parts are simple to use and typically have comparable costs when considering labor. There is also an additional a key factor in this shift — a supplier program.
This program offers credit towards purchases in exchange for old cores and these cores can be used to remanufacture old parts. Managing this process can be complicated for aftermarket parts managers and fleet maintenance managers. However, it doesn’t have to be.
WHAT IS A REMANUFACTURING CORE EXCHANGE PROGRAM?
A remanufacturing core exchange program is a system for swapping used parts for refurbished ones. A core program typically starts when a customer buys a re-manufactured part. Many parts of a diesel engine can be remanufactured since the original components produced during manufacturing are quite costly. There’s a significant amount of casted material that would be wasted without recycling. While some end customers prefer new parts in the aftermarket, most are primarily focused on getting back on the road as quickly as possible.
When a customer decides to buy a re-manufactured part, they usually need to return the old core to receive credit. The core is sent back to the manufacturer to evaluate its eligibility. This is where many differences between core programs emerge. Different suppliers apply varying levels of detail and nuance when assessing the eligibility of the core for reuse.
Common procedures in a reman core exchange program.
– A customer buys a re-manufactured part.
– Customer returns an old core for credit.
– Core has been sent to the manufacturer.
– The manufacturer is responsible for assessing credit eligibility.
– Credit from the returned core has been provided by the customer.
– Reusable core components are included in the re-manufacturing process.
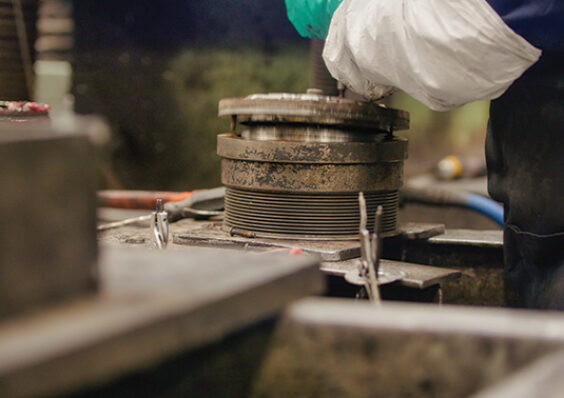
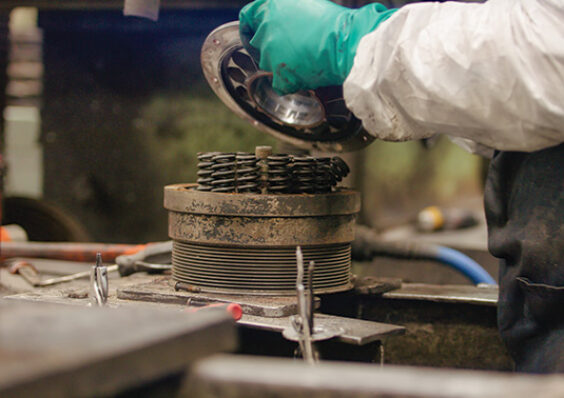
There are many uncertainties that can lead to difficulties for parts managers and technicians. If the core is found to be reusable, the customer will receive credit. The reusable core is then processed for remanufacturing, which usually includes disassembling the old core, validating its parts, cleaning, inspecting, rebuilding it with original equipment components, and conducting quality checks. Not all core programs are created equal. Not all core programs — and remanufactured parts, for that matter — are the same. There are many advantages to consider.
For heavy-duty parts, a core program can help reduce the overall cost of repairs. Remanufactured parts also save on labor time compared to using a rebuild kit, allowing repair bays to operate more efficiently and maximizing equipment uptime. Using a remanufactured fan clutch to replace a damaged one can save 1-2 hours on each repair process. Using alternatives like a repair kit also raises the chances of making mistakes. Remans benefit the environment by reducing the amount of metal that gets scrapped and ends up in landfills. It can be complicated, particularly when working with suppliers that provide different credit levels based on the part’s location. Horton previously offered full, half, or no credit based on the condition of a fan clutch core.
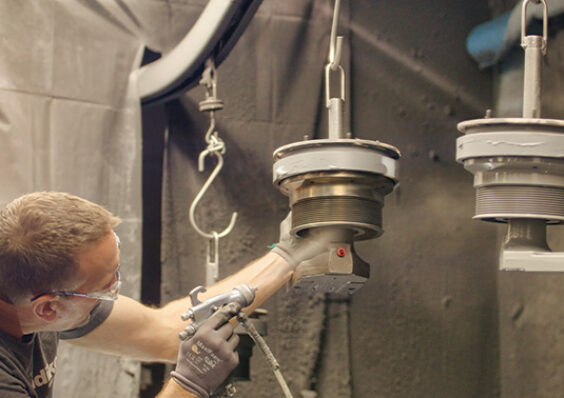
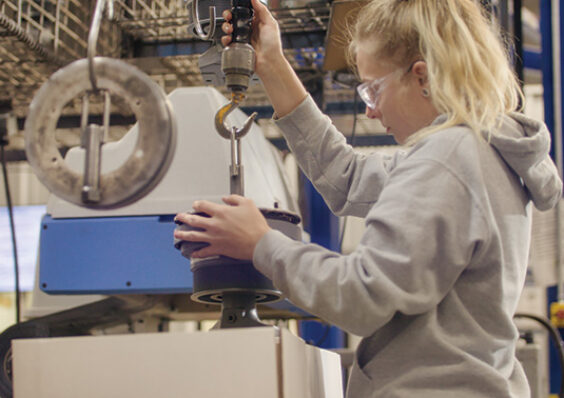
From 2021 onward, the policy has been streamlined to provide either full credit or no credit, provided the core is not physically modified; we accept them and give full credit toward a new reman purchase. Unacceptable damage includes activities like welding and sawing. While some technicians may use creative methods to remove parts, these modifications can make the core unusable according to the supplier’s quality standards. Certain core programs necessitate a „like-for-like“ exchange. To get credit for a new remanufactured part, customers must return the same brand, and in some instances, the same model, of the part. Horton’s updated core policies allow for accepting all competitor cores without requiring a like-for-like exchange.
Why REMAN in the first place?
As soon as a fleet maintenance technician or local truck repairman brings in a damaged part, the clock starts ticking. How quickly can you work with him to get the truck back up and running? And how much does it cost? When a fleet maintenance technician or local truck repairman delivers a damaged part, the process begins. How efficiently can you collaborate with him to restore the truck’s functionality, and what will be the expenses involved? According to a recent survey by the American Trucking Associations Technology and Maintenance Council, 60 percent of respondents reported that hiring new technicians is their top concern.
While using remanufactured parts doesn’t fully address this issue, it can assist teams that are short-staffed in operating more efficiently. Considering core credit and labor, the total cost is generally about the same as a manual rebuild. If you want to go a little deeper into this topic, check out one past discussion on our, reman core fan clutch programs.