How engine cooling systems impact construction equipment design and operation
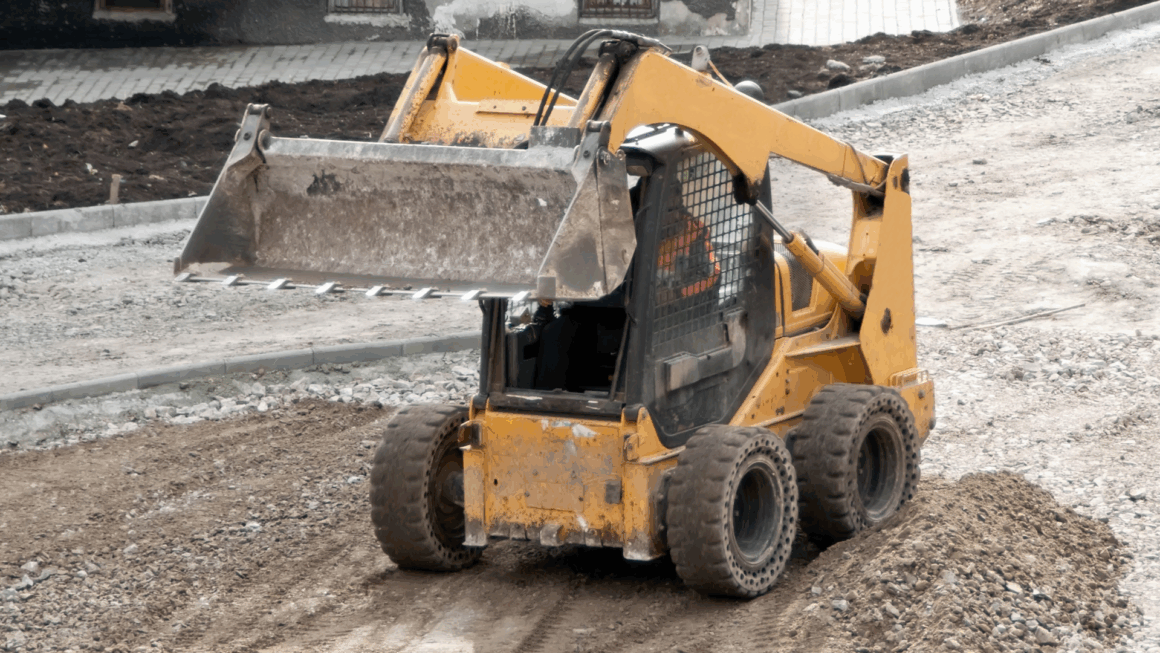
September 9, 2020
Thanks to the ingenuity of engineers at places like Caterpillar, John Deere, CNH, Bobcat, Komatsu and many other OEMs, there are about as many different types of construction machines as there are jobs to be done.
From the smallest compact excavator to the largest road grader, construction machinery frankly provides some of the coolest applications of high-level engineering on the planet. There’s a reason kids push dump trucks around their living rooms and stand mesmerized when a backhoe loader operator is doing his thing in their neighborhood.
To be worth the investment for those inclined toward digging in the dirt, construction gear obviously has to withstand the rigors of extreme temperatures and terrain. It also has to meet increasingly stringent emission and noise regulations.
And what’s not apparent, even after hours of standing at a job site watching these big machines do work, is that the fan, fan drive and other cooling components inside them can make a world of difference in that regard.
Cool and clean
The engine on a skid steer, loader or excavator wouldn’t last long in most climates without some sort of cooling system. But all that airflow in dirt-filled environments means components are prone to clogging.
[RELATED: Three takeaways from Conexpo/Con-Agg 2020]
Given the tight spaces design engineers have to work with, fans can be mounted in a variety of ways — remotely using hydraulics, on the engine with a fan drive to control fan speed, or — in lighter-duty applications — remotely using electric fan systems. Just like in most on- and off-highway equipment, the fan turns to absorb air from the radiator and provide it to the rest of the engine.
This obviously keeps the machine from overheating. But when done properly — that is, not turning faster than it has to, or more often than it has to — the fan can mitigate the amount of debris that makes its way to the engine.
The most effective way to do this? Use a variable-speed fan drive that receives signals from the engine ECM and delivers precise cooling.
This can even help in cold weather; Horton’s viscous-operated LCX fan drives, for example, hold oil in the reservoir when the engine is off. This allows the fan to disengage faster upon startup, which means quicker operation and cab warmup.
Ruling the rules
Greenhouse gas laws have changed the game when it comes to construction. In addition to getting jobs done effectively and on time, owners and operators must ensure compliance with all local and federal emissions laws.
In the United States, that means Tier 4 Final NOx and particulate matter standards that have been in place since 2015. The European Union is currently implementing Stage V of its non-road mobile machinery regulations.
What’s this have to do with engine cooling? A lot, actually. By avoiding excess cooling, engines can both cut down on particulate matter emissions and provide more energy for powering the vehicle. That’s more efficient for the world’s builders and demolition specialists, and beneficial for the environment.
What’s that sound?
The EU has also introduced a directive aimed at reducing noise pollution as its countries become increasingly urbanized. The U.S. isn’t far behind.
Again, this is where a proper cooling package can help. The fan is often the largest source of noise on the vehicle, but its impact can be mitigated significantly by pairing it with a variable-speed fan drive. Other noise reduction measures include specifying a larger fan and running it at a lower speed or taking advantage of specific blade counts, shapes and materials that are designed to emit less noise.
So while no future engineer is likely out there dreaming of delivering adequate airflow or finding the right fan for those awesome yellow behemoths he or she sees on his way to school every day, the cooling components inside them have a significant impact. Both on the ones doing the work and the ones benefiting from it.