10 trends that will impact commercial vehicle manufacturing in the next decade
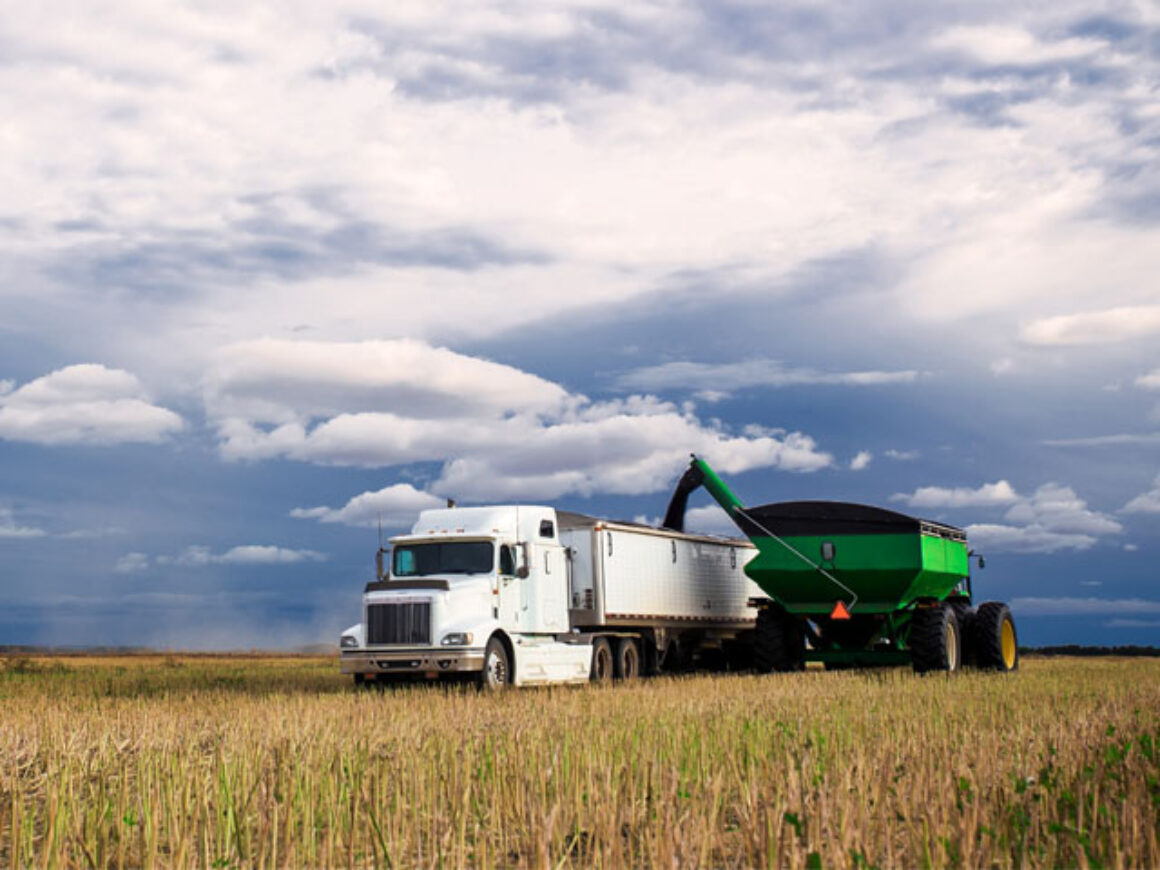
January 6, 2020
In the 2010s, we saw the rapid pace of technological advancement and global economic shifts have a drastic impact on production, sales cycles and what’s possible in the transportation, agriculture, construction, mining and power generation segments.
So what will the next 10 years bring? Here’s a look at what to expect.
What’s coming in the 2020s
1. Electrification will continue to rise, but it won’t take over.
2. Viscous technology will become the primary engine cooling tool in a design engineer or service technician’s arsenal.
3. Emissions regulations will get stricter, but there’s hope for harmonization.
4. Emissions won’t be the only environmental factor on manufacturers’ minds.
5. The compact construction equipment market will grow in leaps and bounds.
6. More new commercial vehicles will run on hydrogen.
7. The rise of the self-driving vehicle will continue.
8. We’ll see more experimentation with, and use of, alternative fuels in existing engines.
9. Access to parts service training will become easier – and more technologically advanced – than ever.
10. Diesel isn’t disappearing.
1. Electrification will continue to rise, but it won’t take over.
Of possibly the most pertinent buzzword in the industry, Horton Vice President of Research and Development Dave Hennessy often says “electrification is the biggest thing coming at us. The real question is how?”
In both the on-highway and off-highway sectors, it’s already here in a lot of ways. Truck manufacturers have more than tinkered with electric semi trucks, and Daimler earlier this year announced the “eCascadia” truck that will begin production in 2021. Volvo, meanwhile, will commence production of electric trucks in Europe as early as March 2020.
But long-haul machines carrying heavy loads require a significant amount of power that’s hard to regenerate while they maintain a constant speed. Stop-and-start applications with short operating ranges like compact construction equipment and smaller delivery vans (think UPS and Amazon) can quickly capture stopping power and retain energy. It’s why Volvo, Caterpillar and other off-highway manufacturers have already debuted electrically-powered compact machines, with plans to expand in the coming years.
Simply finding ways to power heavy-duty equipment using battery power is just the start, though. For electrification to firmly take hold, a vast infrastructure overhaul is required – charging stations, massive fleet conversions and the like. Charging cycles will also affect delivery cycles.
There’s no doubt it’s coming. But experts like Hennessy surmise it’ll take longer than 10 years.
By the end of the decade, your Amazon packages will likely be delivered by an electric-powered vehicle. You may be transported via electric bus at the airport. But the vast number of semis rolling down the interstate will still use internal combustion engines. And before trucks are all electric, a wave of hybrid releases – many in 48V – like the one currently sweeping the automotive market is expected.
The North American Council for Freight Efficiency lays out several arguments for and against battery electric commercial vehicles, identifying weight, cost and infrastructure as the three main issues at stake.

“The transition in specific market segments will be drawn out over decades, sharing space with traditional gasoline, diesel, and other alternative-fuel powertrains and also competing with other emerging technologies like fuel cells and hybrids,” reads a recent NACFE report on electric viability. “Mixed fleets (including diesel, natural gas, hybrid, and BEV products) optimized for specific routes and duty cycles will likely be the norm through 2050.”
A similar trend is expected in construction, agriculture, mining and other off-road segments.
“We expect the same to happen in the off-highway markets,” said Horton Product Manager for Off-Highway Blake Harris. “Applications with shorter operating ranges and lower energy demand (forklifts, compact construction equipment, airport tuggers) will be first to go electric, while applications with high energy demand and long operating ranges will be last (tractors). We will see increased hybridization in the middle (loaders, excavators, off-road lifts).”
2. Viscous technology will become the primary engine cooling tool in a design engineer or service technician’s arsenal.
While electrification – and, in engine cooling terms, providing airflow via electronic means – is coming, the age of fully-variable, viscous fan drives is already here. By regulating the flow of silicon oil within the drive, these clutches can determine exactly how fast to spin the engine fan. The latest, like Horton’s RCV250 for semi truck engine cooling systems and RCV2000 for large-bore mine-haul trucks and the like, communicate directly with the engine’s computer to determine how much cooling is required.
Creating precisely the right amount of airflow within an engine cooling system provides the following benefits over older, legacy technology:
- Fuel efficiency: By providing only the amount of cooling necessary, viscous technology allows engines to dedicate more power to pushing pistons and less to regulating temperature.
- Lower environmental impact: The more efficiently an engine is cooled, the less particulate matter is released into the air, which can significantly decrease carbon emissions.
- Lower noise: Noise pollution will continue to be more heavily regulated in the United States as it already is in Europe, and the lower a fan drive runs, the less noise the machine emits (see item No. 4 on this list).
- Handling the elements: Easier start-up in cold weather conditions and swifter response to extreme temperature changes due to weather.
The European Union’s transportation industry has relied primarily on viscous tech for the past decade, and American manufacturers are expected to follow suit with new truck builds. In construction, mining and ag, viscous engine cooling technology is already becoming the norm.
But on-off clutches, such as the Horton DM Advantage, aren’t going away any time soon. Some trucks’ drives are disengaged up to 90 percent of the time and run at low input speeds, so a fully-variable solution doesn’t offer the same type of savings. On-offs are also simple to install, can be re-built and don’t need to be programmed the way viscous clutches do.
HORTON’S LATEST SERIES OF VISCOUS FAN DRIVES ARE COMPATIBLE WITH A WIDE VARIETY OF ON- AND OFF-HIGHWAY APPLICATIONS.
3. Emissions regulations will get stricter, but there’s hope for harmonization.
Emissions regulations and the massive waves of change they bring will only be elevated during the next 10 years as suppliers, manufacturers, end users and governments work together to reduce the industry’s carbon footprint.
Internationally, that means a lot more harmonization. Currently, the European Union is in the sixth stage of its regulations for heavy-duty diesel engines and has been since 2012. The United States’ greenhouse gas emissions for commercial trucks and buses have begun to enter their second phase, with full implementation coming in 2027.
Off the road, the EU is currently phasing in Stage V for non-road mobile machinery; it’ll be fully enforced by 2021. Meanwhile, the United States has been in Tier 4 of its NOx and particulate matter emissions standards since 2015, with no immediate updates on the horizon.
Then there’s California.
Exempt from the EPA’s Clean Air Act since the 1960s, the Golden State – and a handful of other states following suit – always has stricter emissions regulations than the rest of the country. These tend to follow Europe’s lead sooner than the rest of the U.S.; the EU’s standards are usually about 10 years ahead of North America’s.
And while all these domino effects create a bevy of different CO2 outputs that can’t be surpassed, industrial players like China and Japan have their own sets of standards. As the economy becomes more global and major transportation companies do business in more locales, it’ll be incumbent upon both manufacturers and governments to streamline requirements. This will allow production facilities to scale more efficiently and better serve the world’s collective transportation needs.
With accords like the United Nations’ Paris Agreement, we’re already well on our way. The California Air Resources Board (CARB) and EPA also intend to implement regulations similar to California’s current standards by 2027.
In the meantime, truck, tractor and power generator manufacturers will continue to seek every possible means of reducing emissions – including using fan drives that only spin when they need to.
There are at least tools engineers can use for understanding emissions regulations. The EPA’s greenhouse gas emissions model (GEM) is a desktop application that estimates emissions and fuel efficiency performance based on specific aspects of heavy-duty vehicles. The EU has a similar program called the vehicle energy consumption calculator (VECTO).
According to VECTO, an electronic viscous fan drive mounted to a crankshaft provides the lowest emissions score – which, in this case, is a good thing – for a cooling package.
4. Emissions won’t be the only environmental factor on manufacturers’ minds.
The European Commission estimates the ratio of the world’s urban population will increase from 55 percent in 2018 to 68 percent by 2050, representing an almost 50-percent increase in the world’s urban population. Europe’s level of urbanization is expected to increase from today’s 74 percent to about about 75 percent in 2020 and 83.7 percent by 2050.
So Europe is already on the cutting edge of making sure machines don’t have a negative impact on its citizens’ ear drums. The EU’s Outdoor Noise Directive strictly limits decibel levels for outdoor machinery.
Currently, the EPA doesn’t cover noise for vehicles, but increased emphasis from organizations like the Occupational Safety and Health Administration could change that as time goes on.
This is another space a fully-variable fan drive can help. The EU, for example, allows engine producers to rate vehicle noise with the fan running at 70 percent of input. With a viscous clutch in place, this will create about ¼ of normal sound output – which allows engine manufacturers to pass tests and, more importantly, ensures customers and their local communities will avoid burdensome noise pollution.
Smaller, more efficient fans, such as Horton’s LS5, can also decrease noise especially when combined with a fully-variable drive.
5. The compact construction equipment market will grow in leaps and bounds.
According to OEM Off-Highway, the world’s compact construction equipment market (compact excavators, skid steers, compact track loaders and compact wheel loaders) was valued at more than U.S. $10 billion in 2017 and is likely to reach more than U.S. $15 billion by the end of 2025.
The main reasons: versatility and cost effectiveness.
“Compact wheel loaders are service machines that can support any segment, from landscape and gardening to road, civil engineering and agriculture,” Volvo CE Compact Wheel Loader Business Platform Leader Helmut Broy told OEM Off-Highway. “They are essential multi-tool carriers required for today’s diverse business landscape.”
6. More new engines will run on hydrogen.
While electrification continues to gain momentum, hydrogen fuel cell technology already has it. Nikola claims its hydrogen-powered trucks are emissions-free, and companies like Deutz and Hyundai are exploring options as well.
It’s important to note that whether a vehicle is powered by diesel, hydrogen or some other means (see item No. 8 on this list), it still requires the same type of cooling. Most fan drives run off the engine’s drive shaft and/or computer, so companies like Horton are well equipped to deal with these advancements.
7. The rise of the autonomous vehicle will continue.
Regardless of engine type, every application needs an operator.
Even if it’s a virtual one.
Many companies continue to experiment with self-driving deliveries. The benefits could include safer roads and better fuel economy, but the move to driverless trucks and construction equipment, for example, is still a long way off.
According to the NACFE, “Advancements in technologies that enable vehicles to be self-driving have progressed significantly in the past few years. Demonstrations around the globe are proving that this is possible for all types of vehicles from personal mobility passenger cars to many forms of commercial vehicles, and will have many safety, efficiency, and utilization improvements.”
8. We’ll see more experimentation with, and use of, alternative fuels in existing engines.
By now, many of us have seen the Exxon Mobil ad about how the multinational oil and gas corporation is growing algae to use for fuel. Other biofuels like ethanol or renewable resources like those created via the Fischer-Tropsch process not only reduce emissions but can be used in today’s engines and/or added to today’s fuels for immediate results.

Other industries, such as refuse transportation, have found ways to use methane from waste to create synthetic, renewable fuels.
Why is this important? Per OEM Off-Highway, in order to reach the Paris Agreement’s call for global warming to be limited to 2 above pre-industrial levels, the fossil CO2 emitted by road vehicles must be nearly eliminated over the next three decades. But about half the vehicles that’ll be on the road 10 years from now have already been sold, putting a premium on technology that can be dropped in to existing engines.
9. Access to parts service training will become easier – and more technologically advanced – than ever.
In the on-highway aftermarket, in-person training modules and online learning programs have become the norm. They’re a great way for suppliers to teach diesel technicians and dealers how to service their products.
But it’s about to get even easier.
In the age of the YouTube mechanic, there’s become an increasing demand for easy, simple-to-understand video training. More of that is coming, along with some potential digital solutions that go even more in depth.
Augmented reality – tech that superimposes a computer-generated image on a user’s view of the real world – and virtual reality – fully-immersive, three-dimensional simulations a user can interact with in a seemingly real and physical way – are becoming cheaper and more widely accepted. By 2030, it’s possible at least some service shops will be using these tools to keep pace with the ever-evolving trucking technology landscape.
10. Diesel isn’t disappearing.
Far from it, in fact.
While several geopolitical factors have impacted manufacturing as a whole, diesel manufacturing remains strong, particularly in the U.S. The latest diesel technologies are getting closer and closer to zero emissions, and jobs in the sector continue to grow.
U.S. Bureau of Labor statistics indicate a job-growth outlook of five percent each year.
While it’s impossible to predict the future, it’s safe to say the wheels of change will keep turning in the 2020s. Those who keep pace will have identified technologies and components that can help their applications run more efficiently while making the world a safer place to live and operate.