Optimized engine cooling can reduce fuel consumption
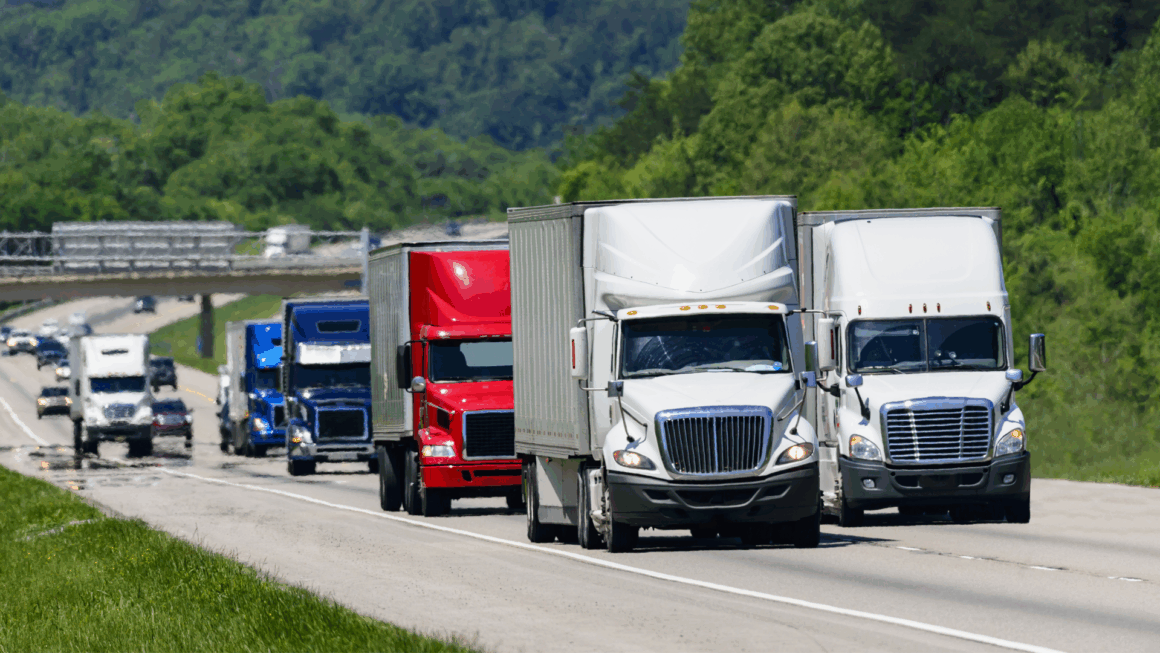
June 15, 2020
A local TV news headline in Memphis once read “snow to turn to water as sun comes out.” Workers once put an “out of order” sign above the hole they left when removing a school drinking fountain. A decal outside a pharmacy asks patrons to “open door before entering.”
And engineers put a fan on diesel engines to keep them from overheating.
Obvious stuff, right? But what’s not as readily apparent is that engine cooling systems can have a direct impact on fuel economy, in addition to making sure under-hood components don’t literally melt while a truck is heading down the interstate.
The simplest internal combustion engines feature a fan connected directly to the engine’s crankshaft. The shaft spins to power the engine, and the fan turns at the same speed to deliver cooling.
But what it doesn’t do is power down once the engine has reached an optimal temperature. That’s where a fan clutch comes in. Fan clutches, also called fan drives, regulate fan speed by “communicating” with the engine and spinning the fan slower when appropriate.
On/off fan clutches are self-explanatory; once the engine is at the right temperature, the fan shuts off. Two-speed drives are a little more advanced, offering a pair of different fan speeds based on how much cooling is required.
The latest fan drive technology is called variable-speed, which delivers precise cooling by featuring a potentially unlimited number of fan speeds.
Older, pneumatic fan clutches react to changes in air pressure to determine whether to be in on, off or low-speed mode. Variable-speed drives use viscous technology controlled either by an engine’s computer, or sensors that respond to engine temperature needs in real time.
No matter what type of clutch is used, the more a fan turns only as fast as necessary, the easier it is for the truck to move while using less energy. That means fuel savings and a more efficient engine overall.
And don’t underestimate the power of the fan. By tweaking the number, angle, pitch width and length of blades, design engineers can help carry more air through a truck’s radiator and into the engine compartment. The more precise the fan design, the quicker the fan can turn slower and the sooner the engine shaft can direct more energy toward powering the vehicle.
For example, when Kansas City fleet Olinger Heavy Hauling upgraded to a Horton RCV 250 fully-variable, viscous fan drive, it saw a 15-percent increase in fuel savings on its Kenworth T800 trucks.
The same technology can be applied to a variety of off-highway applications, including construction equipment, agricultural tractors and large-bore mine haul trucks.
While results vary based on a number of factors, it’s perhaps a best-kept secret that optimized engine cooling can lead to significant fuel savings.